Präzises und genaues Schneiden ist ein wesentlicher Bestandteil eines jeden Metallverarbeitungsunternehmens – und das aus gutem Grund.
Ein sauberer, exakter Schnitt ermöglicht präziseres Schweißen und weniger Zeitaufwand für Schleifen und Nacharbeiten.
Aber es ist keine leichte Aufgabe, einen qualitativ hochwertigen Schnitt zu erzielen.
Ein weiterer wichtiger Aspekt bei der Verbesserung der Produktionseffizienz ist die Steuerung des Materialflusses in Ihrer Werkstatt, um den spezifischen Anforderungen gerecht zu werden. MMC Contractors, ein in den USA ansässiges Maschinenbauunternehmen, hat erkannt, dass dies der Schlüssel ist, um mit dem Wachstum der Projekte Schritt zu halten.
Mit dem Wachstum kamen die Wachstumsschmerzen
Als MMC schnell wuchs, überstiegen die Projekte die Möglichkeiten der damals 17.000 Quadratmeter großen Werkstatt. Janning und der heutige Leiter der Rohrfertigung, Matt Townsend, sagen, dass die Aufträge mit der kleineren, primitiveren Einstiegsmaschine, die sie zu Beginn verwendeten, zeit- und arbeitsintensiv waren. Die Maschine verfügte über ein Rollensystem mit einachsiger Schneidefunktion und war weder auf Geschwindigkeit noch auf Genauigkeit ausgelegt. Das bedeutete oft, dass 42-Fuß-Rohre gerollt werden mussten, die manuell auf Schrägen und Winkel eingestellt und von Hand geschnitten wurden.
Der Vorarbeiter von Steamfitter, Justin West, sagt, dass dies oft zu einer Reihe von ungleichmäßigen Schnitten führte.
„Als wir diese Teile von Hand gemacht haben, hatten wir etwa 1,5 Meter Spielraum“, erklärt er.
„Die Schnitte waren nicht so präzise.“
„Wir wollten unseren Prozess automatisieren“, erklärt Janning.
„Das Gebäude nebenan stand zum Verkauf. Das war ein entscheidender Moment. Wir brauchten aber eine Maschine, die in den Raum passte.“
Insbesondere brauchten sie eine Maschine mit einem Entladesystem, das seitlich ausgerichtet war.
So konnten sie die Rohre in den Fluss der Werkstatt entladen.
Das Team von MMC kannte zwar eine Rohrprofiliermaschine von HGG Profiling Equipment, die vieles von dem versprach, was sie von einer Plasmaschneidmaschine erwarteten, einschließlich Langlebigkeit und erhöhter Präzision und Genauigkeit, aber das Standardmodell war einfach zu groß für ihren Platz, und die Größe war nicht die einzige Sorge.
Es bot nicht die benötigte Seitenentladung und würde wertvolle Zeit kosten, um die Bediener für die Bedienung zu schulen – so dachten sie zumindest.
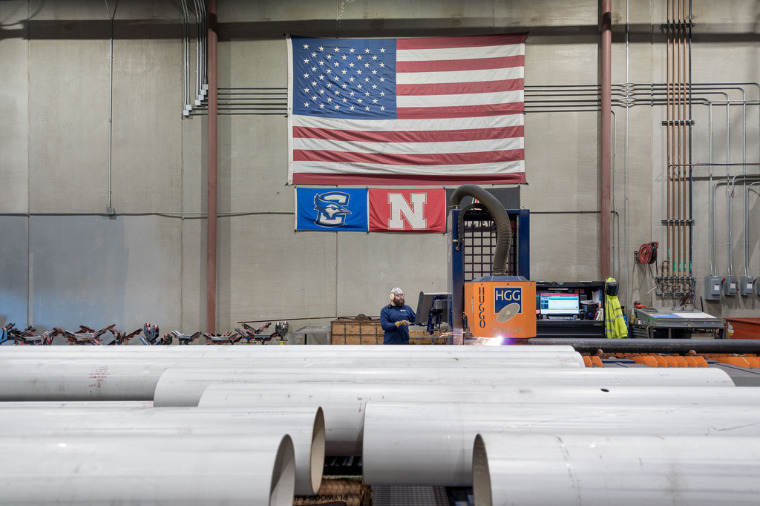
Das Team beschloss, sich mit HGG zu treffen, um die Optionen zu besprechen.
Laut West hörte sich HGG die Wunschliste der gewünschten Funktionen und Maschinenfähigkeiten genau an und ließ sich von der Notwendigkeit einer einzigartigen Lösung nicht abschrecken.
„Als wir das Design besprachen, kamen sie in unsere Büros und fragten: ‚Was brauchen Sie?'“
bemerkt Janning.
HGG bot an, eine Maschine zu entwerfen und zu bauen, die zu den Platzverhältnissen passte – eine Maschine mit einem einzigartigen Einzug und einem Seitenauswurf – und im November 2020 kaufte und installierte MMC den vollautomatischen, maßgeschneiderten ProCutter 900 RB.
Sofortige Zeit- und Materialeinsparungen
Das Ergebnis war eine sofortige, fast sofortige Zeitersparnis.
Ein wiederkehrender Auftrag mit einem 30-in.
Rohr, dessen Zuschnitt vor der Installation der neuen Maschine zwei Wochen dauerte, ist jetzt in nur vier Tagen erledigt.
Die Konfiguration mit der Einzugsfunktion erwies sich als „unglaubliche Ergänzung“, die die Art und Weise, wie die Rohre in die Werkstatt gebracht werden, verändert, sagt West.
Das Einlaufbett mit Außenförderer und das seitliche Auslaufbett am Rohrprofilierer in der Werkstatt haben den gesamten Arbeitsablauf rationalisiert.
Außerdem gibt es viel weniger Ausschuss.
Die Software ist so programmiert, dass zwischen den Schnitten etwa 0,5 Zoll abfallen.
zwischen den Schnitten.
In Verbindung mit der Möglichkeit, das Rohr so zu optimieren, dass die meisten Schnitte pro Länge möglich sind, wird die Menge des anfallenden Ausschusses drastisch reduziert.
„Die Möglichkeit, Rohre in verschiedenen Größen auf der Zuführung zu stapeln und sie einfach zur Hand zu haben und die Stücke nach Bedarf einzurollen, hat die Materialhandhabung wirklich reduziert, ganz zu schweigen von den dafür benötigten Arbeitskräften“, erklärt West und fügt hinzu, dass dies für eine Fertigungsstätte, die etwa 8.000 Schweißnähte pro Jahr (durchschnittlich 40.000 Schweißnähte) an Rohren mit einer Größe von 1/2 Zoll bis 48 Zoll herstellt, ein wichtiger Vorteil ist.
Geben Sie den CAD-Entwurf direkt in die Maschine ein
Der Herstellungsprozess ist nicht nur insgesamt weniger anstrengend, sondern auch viel effizienter.
Mit dem maßgefertigten ProCutter werden die Rohre automatisch mit vorberechneter Präzision und Geschwindigkeit über das Rollenbett zum Hauptantrieb geführt, so dass die fertigen Profile mühelos hergestellt werden können.
„Wir entwerfen sie im CAD, übertragen sie vom CAD in die Maschine und wählen dann die gewünschten Profile aus, drücken einen Knopf und die Maschine schneidet sie auf einmal“, sagt Townsend.
Sicherheit der Mitarbeiter als Priorität
Glücklicherweise bedeutete die erhöhte Produktivität kein erhöhtes Risiko für das Team aus Dampfschlossern, Klempnern und Blechbearbeitern.
Das ist zum Teil einem Luftreinigungssystem zu verdanken, das in der neuen Maschine enthalten ist – eine Funktion, auf die HGG bestanden hat, obwohl sie in den Vereinigten Staaten nicht vorgeschrieben ist.
Das System filtert Partikel und Feststoffe heraus, die einfach aus einer Schublade im Luftwäscher entleert werden können.
„Wir hatten vorher nie über Luftreinigung nachgedacht“, gibt West zu.
„Durch die Installation des Luftreinigungssystems haben wir die Fertigungshalle verändert. Sie ist so sauber. HGG würde die Maschine nicht ohne sie bauen.“
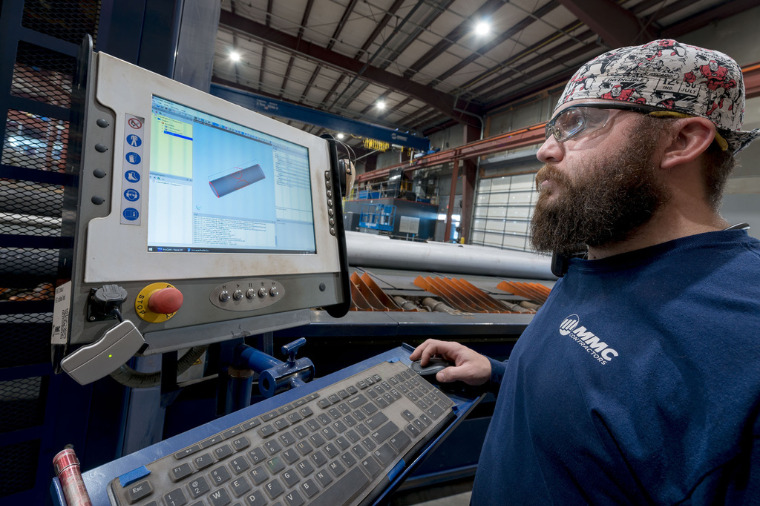
Der Herzschlag des Ladens
Die Maschine, die Janning liebevoll als „Herzstück der Werkstatt“ bezeichnet, ist sicher zu bedienen und langlebig und macht die tägliche Arbeit erst möglich.
Der Wechsel von einer primitiven Handschneidemaschine zu einem vollautomatischen, maßgeschneiderten Arbeitspferd, „das alles kann“, hat nur ein Problem geschaffen, sagt Janning – er kann sich nicht vorstellen, anders zu arbeiten.
„Ich glaube, wir haben uns mit dieser Maschine irgendwie verwöhnt; es wäre sehr schwierig, ohne sie auszukommen.
„Alles hier beginnt mit dieser Maschine“, schließt West.
„Ohne sie wären wir fast zum Stillstand gekommen.“